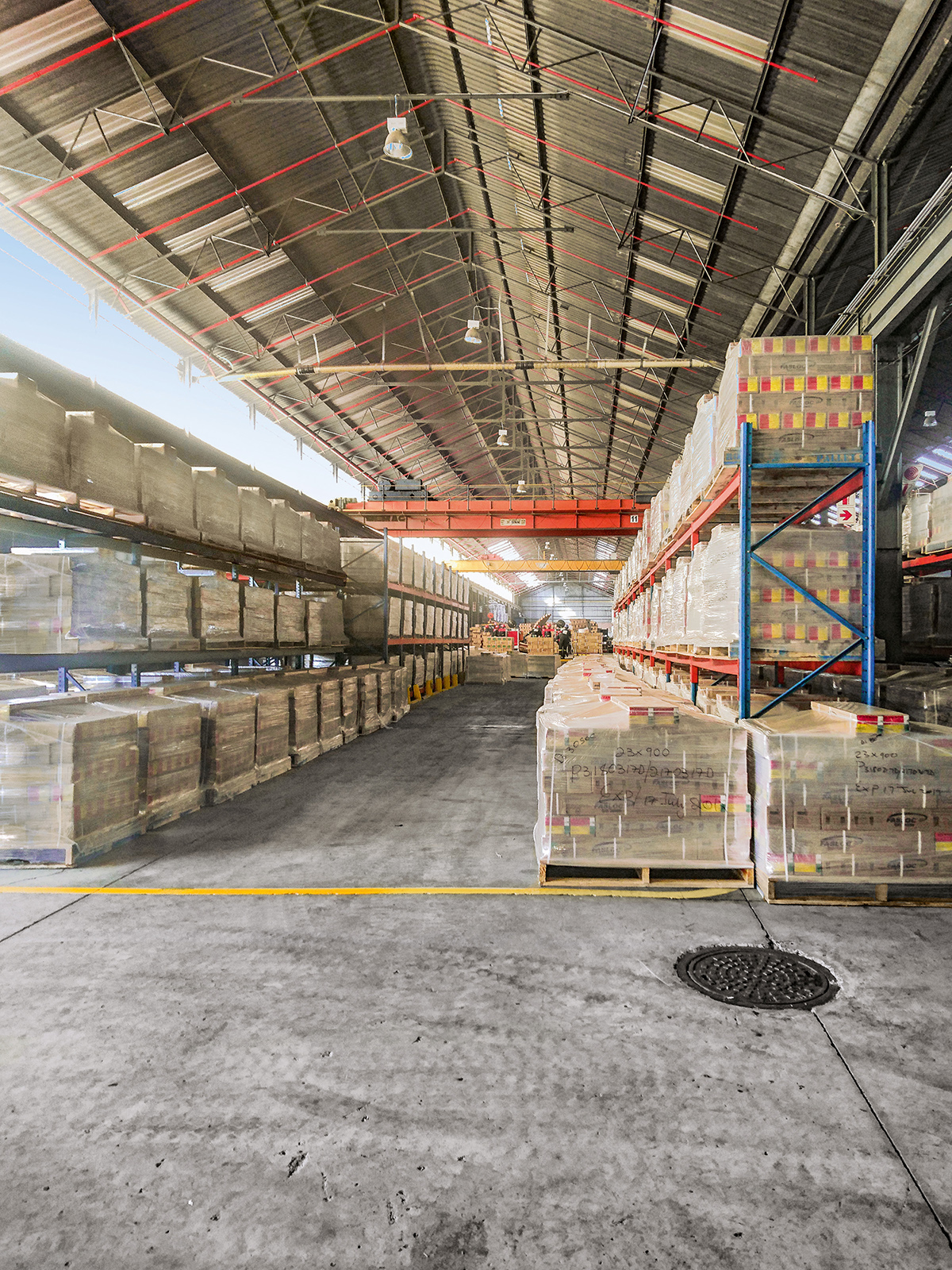
Rocbolt Technologies baut Kunstharz-Produktion in Südafrika aus
Vor Kurzem wurde im Werk der Rocbolt Südafrika in Kempton Park bei Johannesburg eine Untersuchung durchgeführt, um ineffiziente Vorgänge zu identifizieren. Es mussten mehrere Faktoren in Angriff genommen werden, um Rocbolts Ziel einer nachhaltigen Steigerung der Produktion zu erreichen. Zudem mussten einige wichtige Systemfunktionen geändert werden, um den korrekten Prozessfluss zu gewährleisten.
Die Studie beinhaltete die folgenden wesentlichen Aspekte:
Produktion
- Es war bisher aufwändig, das Kunstharz vom Vormischen zu den Kunstharz-Produktionsmaschinen zu befördern
- Die Kunstharz-Produktionsmaschinen sind spezifischen CFD-Maschinen zugeordnet, so dass sie nur begrenzt austauschbar waren
- Beauftragung eines Kunstharz-Silos
Logistik
- Der Standort bietet nicht genügend Platz, um die gewünschte Zahl von Lastwagen pro Tag zu be- und entladen
- Hohe Transportrate wegen kleiner Lasten, hauptsächlich verursacht durch Platzbeschränkungen an der Verladerampe
Im Rahmen der Erweiterung wurde zunächst der Produktionsprozess optimiert. Dies beinhaltete auch Produktionsbehälter, mit deren Hilfe die Produktion der Kunstharz-Patronen vom eigentlichen Verpackungsprozess vollständig getrennt werden konnte.
Zudem wurde der tägliche Transport der produzierten FASLOC®-Kunstharzpatronen zum Verpackungs- und Logistikzentrum optimiert. Der komplette Verpackungsprozess wurde hier in ein eigenes Lager verlegt. Im Rahmen des Umzugs wurden alle Steppmaschinen für die Verpackungen aus der Produktion verlagert.
Die laufende Produktion von Kunstharz-Patronen wurde in vier neue, komplett getrennte Produktionslinien aufgeteilt. Weiterhin installierte man Rohrleitungen und zwei neue Vormischungs-Tanks, so dass die bereits bestehenden Tanks 3 und 4 entfernt werden konnten.
Um eine kontinuierliche Überwachung der kompletten Produktion für die Qualitätskontrolle zu gewährleisten, wurde zusätzlich eine Hauptkontroll-Station mit 4 Touchscreens installiert.
Darüber hinaus wurden die Betriebsgebäude instand gesetzt, die Silos mit Füllstand-Sensoren ausgestattet, und die kompletten Verpackungsmaschinen wurden in ein eigenes Verpackungs- und Logistikzentrum umgezogen, welches dem Stahlwerk angegliedert ist.
Dank dieses Maßnahmen-Bündels konnte die Produktivität nachhaltig erhöht und gleichzeitig die Ausschussrate um 3-4% reduziert werden.